VMZINC Attributes
Zinc is among the most sustainable metals used in construction today and has been used on the roofs of Paris for almost 200 years.
Physical Properties of Titanium Zinc by VMZINC | |
---|---|
Density | 7.18 t/m3 |
Thermal expansion coefficient (parallel to the rolling direction) | 0.022 mm/m/ºC |
Melting Point | 420ºC |
Recrystallization point | 300ºC |
Heat conductivity | 110 W/(mK) |
Electrical conductivity | 17 MS/m |
Danger of sparking | Non-sparking |
Magnetic properties | Diamagnetic |
Weights of Different Zinc Thicknesses
Thickness (MM) | Gauge | Thickness (inches) | Weight (kg/m2) |
---|---|---|---|
0.7 | 24ga | 0.027 | 5.026 |
0.8 | 22ga | 0.032 | 5.744 |
1.0 | 20ga | 0.039 | 7.180 |
1.5 | 16ga | 0.059 | 10.770 |
All weights are calculated using a density of 7.18t/m3 or 1mm = 7.18 kg/m2
Zinc
Alloy Composition (to EN 988) | |
---|---|
To EN 1179 (with SHG 99.9995% purity) |
Other elements making up the alloy are:
Copper | 0.08 – 1.0% |
Titanium | 0.06 – 0.2% |
Aluminium | ≤ 0.015% |
Zinc Sheet Tolerances (To EN988) | |
---|---|
Thickness | ±0.03mm |
Width | 0 to +2mm |
Length | 0 to +10mm |
Flatness of Sheeting | ≤ 2mm (See additional omega rule below) |
Omega rule for acceptable flatness of VMZINC sheets
The omega (ω) rule is expressed as: ω = 100 x h/l
where: ω = < 0.6
wave height is h = 2mm maximum
wave length is l (in mm)
Mechanical Properties (to EN 988) | |
---|---|
0.2% proof strength, non-proportional extension | ≥ 100 N/mm² |
Tensile strength | ≥ 150 N/mm² |
Percentage total elongation at fracture | ≥ 35% |
Bending test at 20ºC | No cracks |
Refolding after bending at 20ºC | No cracks |
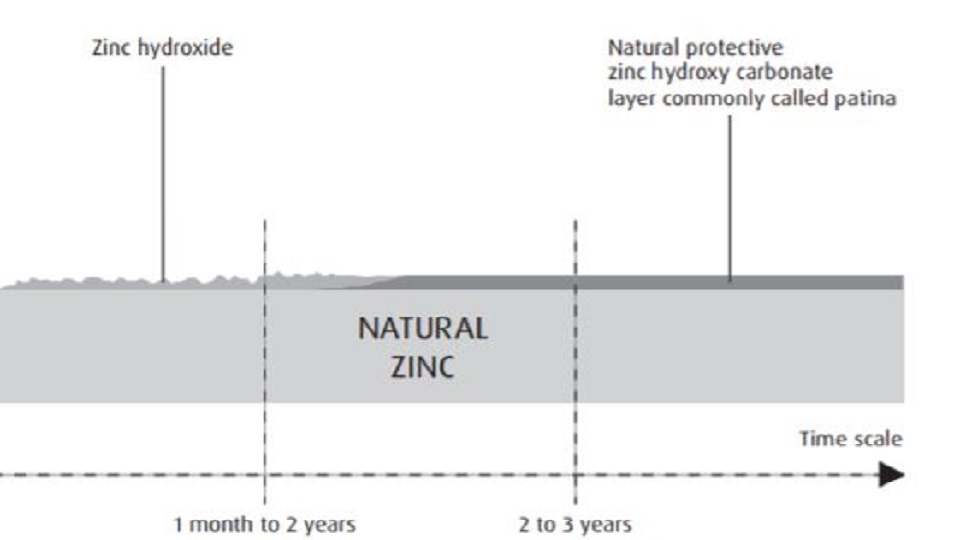
Formation of the natural patina
Zinc reacts with water to form zinc hydroxide; this then reacts with Co2 to form the stable compound zinc hydroxy carbonate. When zinc is exposed to too much water and not enough Co2 the stable grey patina will not form leaving the unstable zinc hydroxide which is commonly referred to as white rust. The amount of time required for formation of the patina from Natural zinc will depend on the exposure of the zinc to water. a low slope roof may only require 3 years whereas a protected soffit may require over 10 years exposure.